Blog
How Predictive Maintenance Reduces Scrap and Downtime
In the fast-paced world of manufacturing, unplanned downtime and excessive scrap are two of the most costly challenges. Traditional maintenance strategies—reactive or strictly scheduled—often fall short, leading to unexpected breakdowns, wasted materials, and lost productivity. Predictive maintenance, powered by data analytics and IoT, is transforming how manufacturers manage their assets, delivering measurable reductions in both scrap and downtime.
Understanding Predictive Maintenance
Predictive maintenance is a proactive approach that uses real-time data, sensors, and analytics to monitor equipment health and predict when failures are likely to occur. Unlike preventive maintenance, which is performed on a fixed schedule regardless of actual machine condition, predictive maintenance targets interventions only when truly needed—just before a failure would impact operations.
Minimizing Unplanned Downtime
Unplanned downtime is a major drain on manufacturing profitability. When a critical machine fails unexpectedly, production stops, labor sits idle, and expensive rush repairs or parts shipments become necessary. According to industry research, unplanned downtime can cost manufacturers up to $125,000–$260,000 per hour, depending on the industry and process.
Predictive maintenance dramatically reduces these incidents by continuously analyzing equipment performance data. Early warning signs—such as abnormal temperature, vibration, or pressure—are detected by IoT sensors and flagged for attention. This allows maintenance teams to schedule repairs during planned downtimes, order parts in advance, and avoid costly emergency interventions. In real-world cases, manufacturers have achieved up to 40% reductions in downtime after implementing predictive maintenance programs.
Reducing Scrap Through Early Detection
Scrap is often the result of machines operating outside optimal parameters, sometimes for hours or days before a failure is noticed. Predictive maintenance helps minimize scrap by identifying subtle changes in machine behavior before they affect product quality. For example, a misaligned bearing or overheating motor can be detected early, allowing for timely intervention before defective products are produced.
By ensuring equipment always runs within specified tolerances, predictive maintenance supports consistent product quality, reduces waste, and enhances customer satisfaction.
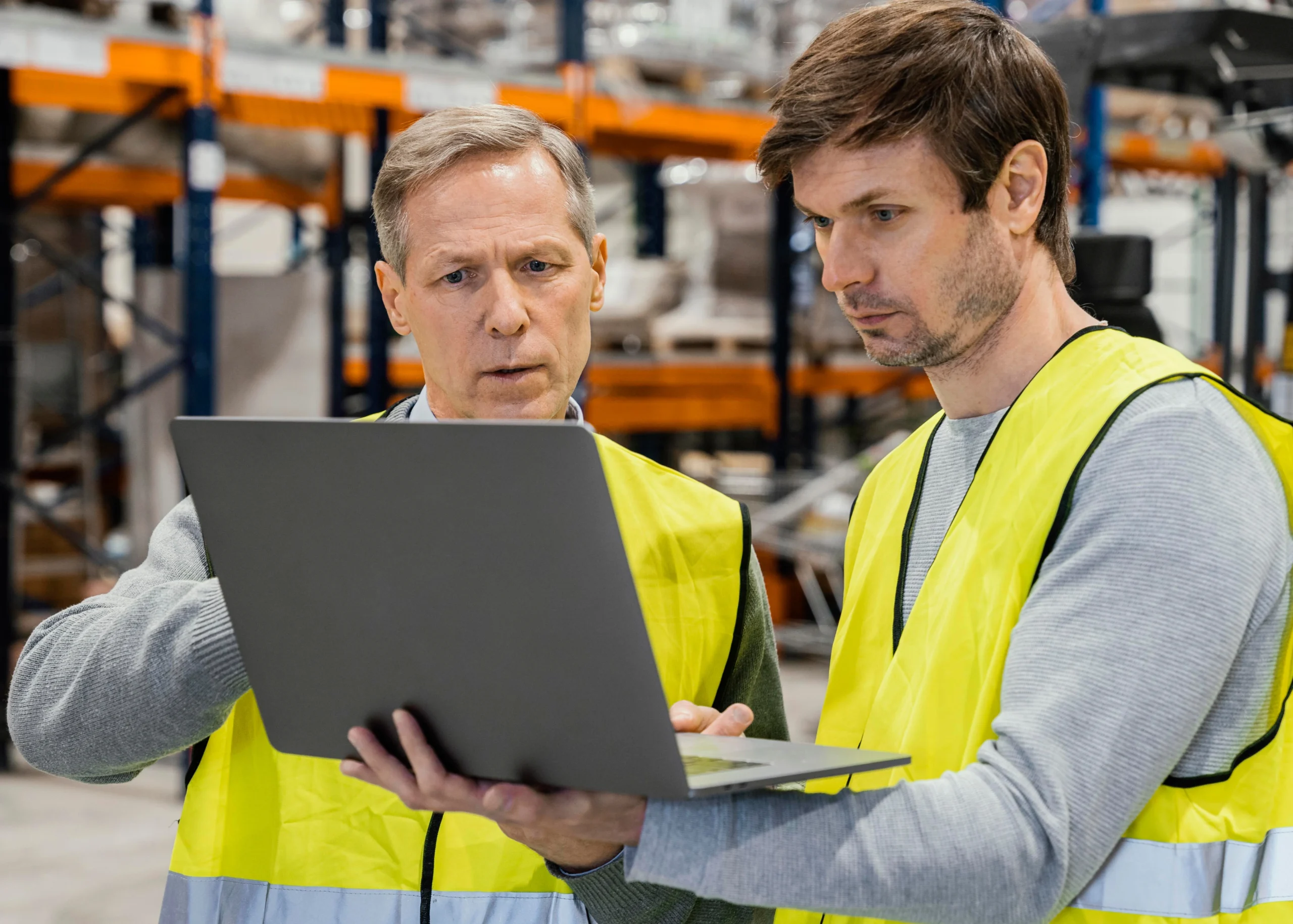
Extending Equipment Life and Lowering Maintenance Costs
Predictive maintenance not only prevents catastrophic failures but also extends the lifespan of critical assets. By addressing minor issues before they escalate, manufacturers avoid the need for premature equipment replacement, maximizing return on investment. Studies show that predictive maintenance can extend equipment life by 20–40% and reduce overall maintenance costs by focusing resources where they are truly needed.
Additionally, predictive maintenance eliminates unnecessary preventive maintenance tasks, freeing up maintenance teams for higher-value work and reducing overtime labor costs.
Optimizing Spare Parts Inventory
Maintaining the right balance of spare parts is a constant challenge. Predictive maintenance provides accurate forecasts of when parts will be needed, allowing for just-in-time ordering and reducing the need for costly emergency shipments or excessive inventory. This optimization leads to 20–30% reductions in spare parts costs while improving parts availability when truly needed.
Building a Reliability-Centered Culture
Beyond the direct financial benefits, predictive maintenance fosters a data-driven, reliability-centered culture. Maintenance and operations teams become more proactive, collaborating to keep equipment running smoothly and efficiently. This shift not only boosts operational confidence but also provides a competitive edge in the marketplace.
Conclusion
Predictive maintenance is more than just a maintenance strategy—it’s a catalyst for operational excellence. By leveraging real-time data and analytics, manufacturers can dramatically reduce both scrap and downtime, extend asset life, and lower costs. As the manufacturing landscape grows ever more competitive, adopting predictive maintenance is essential for staying ahead and achieving long-term success.
Ready to reduce scrap and downtime in your facility? Discover how IoTiView’s predictive maintenance solutions can transform your operations for the better.