Blog
Integrating IIoT with Legacy Equipment
How smart factories are unlocking hidden productivity through real-time visibility and intelligent decision-making.
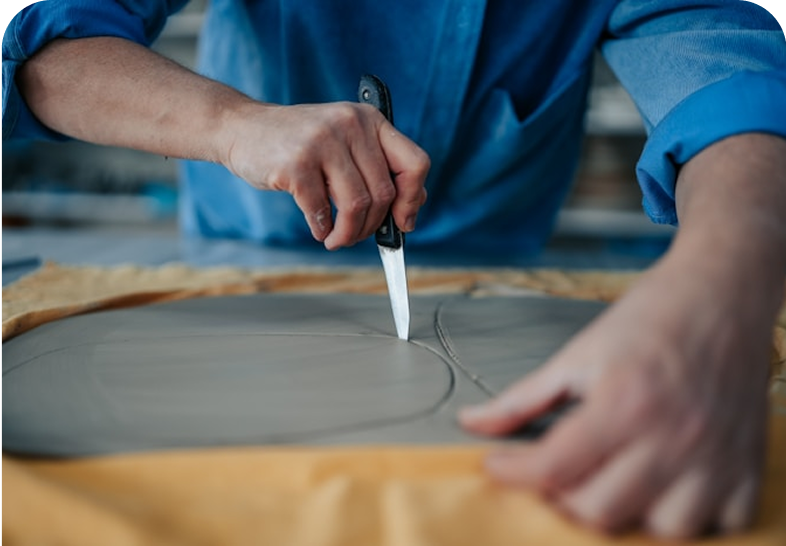
In today’s era of digital transformation, manufacturing is no longer just about making things—it’s about making things better, faster, and smarter. At the heart of this evolution is OEE (Overall Equipment Effectiveness), a gold-standard metric that provides a comprehensive view of production performance. Yet, despite its power, many factories struggle to move the OEE needle.
The answer? A Connected Factory.
What Is a Connected Factory?
A connected factory integrates machines, sensors, software, and people into a real-time digital ecosystem. With Industrial IoT (IIoT), edge computing, and cloud platforms, factories can collect, analyze, and act on data instantly. This connectivity forms the foundation for optimizing OEE at scale.
Why OEE Still Matters
OEE measures how well a manufacturing operation is utilized compared to its full potential. It accounts for:
- Availability (downtime)
- Performance (speed losses)
- Quality (defects)
Even a 5% improvement in OEE can lead to significant cost savings and throughput gains—if you know where to focus.
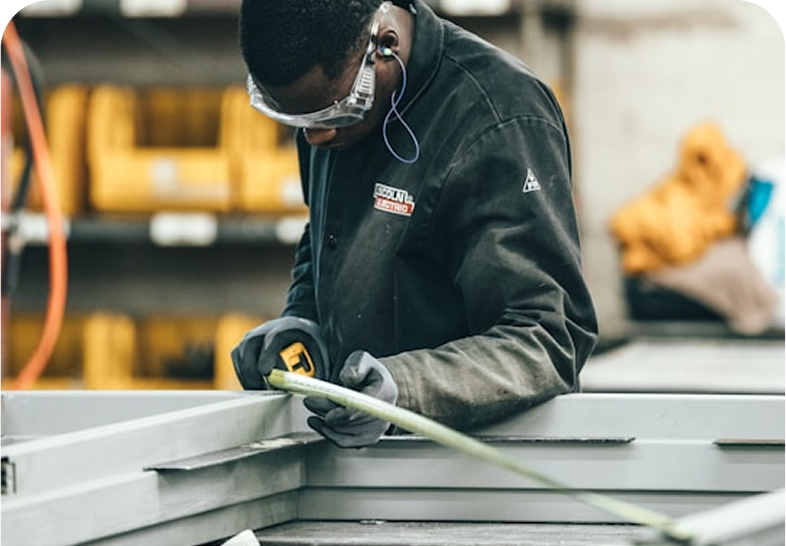
How a Connected Factory Maximizes OEE
1. Real-Time Downtime Tracking
Manual logs and end-of-shift reports are history. With connected machines, downtime events are captured automatically, tagged with root causes, and visualized on dashboards instantly. Operators and supervisors can take corrective action before minor issues become major bottlenecks.
Result: Higher Availability.
2. Performance Monitoring with Live KPIs
Edge devices monitor cycle times and machine speeds in real-time, comparing actual vs. planned performance. Deviations trigger alerts, and advanced analytics detect patterns that might indicate wear, poor calibration, or operator inefficiencies.
Result: Boosted Performance.
3. Automated Quality Insights
Vision systems and AI-based inspection tools analyze product quality without slowing down the line. Feedback loops can adjust process parameters on the fly, reducing defects and improving consistency.
Result: Better Quality scores.
4. Predictive Maintenance Integration
Instead of reacting to breakdowns, connected systems anticipate failures using sensor data (temperature, vibration, current). Maintenance becomes proactive, reducing unexpected downtime and prolonging asset life.
Result: Reduced unplanned Availability losses.
5. Unified Visibility Across Sites
Multi-plant dashboards unify OEE data across regions, product lines, or shifts. This global visibility allows manufacturers to benchmark performance, replicate best practices, and build a culture of continuous improvement.
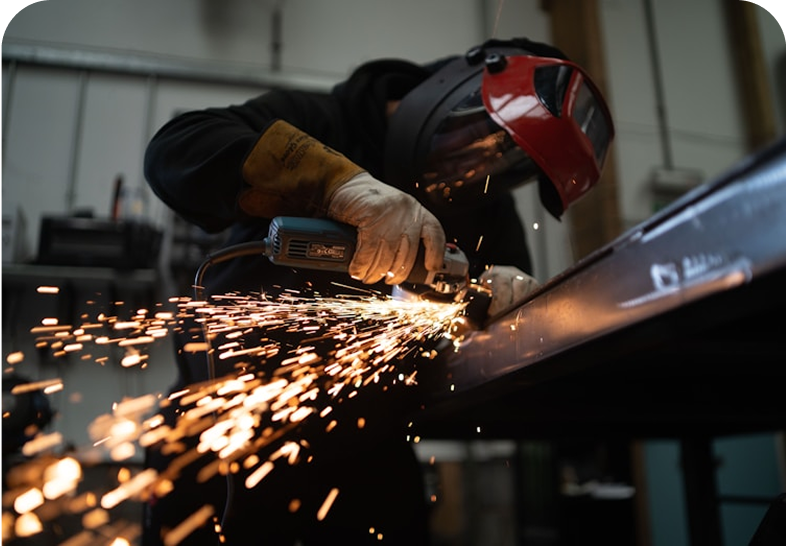
From Data to Action: The OEE Flywheel
A connected factory doesn’t just collect data—it creates a feedback loop that continuously optimizes operations:
- Detect →
- Analyze →
- Act →
- Learn →
- Improve
This flywheel turns faster with automation, AI, and a workforce empowered by actionable insights.
Maximizing OEE in a connected factory isn’t just about hitting a number—it’s about unlocking the full potential of your assets, processes, and people. It’s about turning every data point into a competitive advantage.
Factories that embrace this digital shift are not just more efficient—they’re more resilient, more agile, and more profitable.
Are you ready to transform your factory’s OEE? The tools are here. The insights are real-time. The opportunity is now.